De verkoop van elektrische voertuigen is de afgelopen jaren exponentieel gegroeid, wat gepaard ging met dalende prijzen. De adoptie van EV’s blijft echter beperkt door hun hogere stickerprijs in vergelijking met vergelijkbare gasvoertuigen, ook al zijn de totale eigendomskosten voor EV’s lager.
EV’s en voertuigen met een verbrandingsmotor zullen waarschijnlijk ergens in het volgende decennium dezelfde stickerprijs bereiken. De timing hangt af van één cruciale factor: de kosten van de batterij. Het accupakket van een EV maakt ongeveer een kwart uit van de totale autokosten en is daarmee de belangrijkste factor in de verkoopprijs.
De prijzen van het accupakket zijn snel gedaald. Een typisch EV-batterijpak slaat 10-100 kilowattuur (kWh) elektriciteit op. De Mitsubishi i-MIEV heeft bijvoorbeeld een batterijcapaciteit van 16 kWh en een actieradius van 62 mijl, en de Tesla model S heeft een batterijcapaciteit van 100 kWh en een actieradius van 400 mijl. In 2010 bedroeg de prijs van een EV-accupakket meer dan 1.000 dollar per kWh. Dat is gedaald tot 150 dollar per kWh in 2019. De uitdaging voor de auto-industrie is om uit te zoeken hoe de kosten verder kunnen worden verlaagd.
Het doel van het ministerie van Energie voor de industrie is om de prijs van accupakketten te verlagen tot minder dan $ 100/kWh en uiteindelijk tot ongeveer $ 80/kWh. Bij deze accuprijzen zal de stickerprijs van een EV waarschijnlijk lager zijn dan die van een vergelijkbaar voertuig met verbrandingsmotor.
Voorspellen wanneer die prijsovergang zich zal voordoen, vereist modellen die rekening houden met de kostenvariabelen: ontwerp, materialen, arbeid, productiecapaciteit en vraag. Deze modellen laten ook zien waar onderzoekers en fabrikanten hun inspanningen op richten om de kosten van batterijen te verlagen. Onze groep aan de Carnegie Mellon University heeft een model van batterijkosten ontwikkeld dat rekening houdt met alle aspecten van de productie van EV-batterijen.
Van onderaf
Modellen die worden gebruikt voor het analyseren van batterijkosten worden geclassificeerd als “top-down” of “bottom-up”. Top-down modellen voorspellen de kosten hoofdzakelijk op basis van vraag en tijd. Een populair top-down model dat de kosten van batterijen kan voorspellen is de wet van Wright, die voorspelt dat de kosten dalen naarmate er meer eenheden worden geproduceerd. Schaalvoordelen en de ervaring die een industrie in de loop van de tijd opdoet, drukken de kosten.
De wet van Wright is generiek. Hij geldt voor alle technologieën, waardoor het mogelijk is om de daling van de batterijkosten te voorspellen op basis van de daling van de kosten van zonnepanelen. De wet van Wright laat echter – net als andere top-down modellen – geen analyse toe van de oorzaken van de kostendalingen. Daarvoor is een bottom-up model nodig.
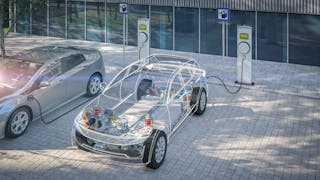
Om een bottom-up kostenmodel op te stellen, is het belangrijk te begrijpen wat er allemaal komt kijken bij het maken van een batterij. Lithium-ionbatterijen bestaan uit een positieve elektrode, de kathode, een negatieve elektrode, de anode en een elektrolyt, evenals uit hulpcomponenten zoals terminals en behuizing.
Elke component heeft kosten in verband met materialen, fabricage, assemblage, uitgaven in verband met fabrieksonderhoud, en overheadkosten. Voor EV’s, batterijen moeten ook worden geïntegreerd in kleine groepen cellen, of modules, die vervolgens worden gecombineerd tot packs.
Ons open source, bottom-up batterijkostenmodel volgt dezelfde structuur als het batterijproductieproces zelf. Het model maakt gebruik van inputs voor het batterij fabricageproces als inputs voor het model, met inbegrip van batterij ontwerpspecificaties, grondstoffen en arbeidsprijzen, kapitaalinvesteringsvereisten zoals productie-installaties en apparatuur, overhead tarieven en productievolume om rekening te houden met schaalvoordelen. Het gebruikt deze inputs om de fabricagekosten, materiaalkosten en overheadkosten te berekenen, en die kosten worden bij elkaar opgeteld om tot de uiteindelijke kosten te komen.
Kostenbesparingsmogelijkheden
Met behulp van ons bottom-up kostenmodel kunnen we de bijdragen van elk onderdeel van de batterij aan de totale batterijkosten uitsplitsen en die inzichten gebruiken om de impact van batterijinnovaties op de EV-kosten te analyseren. Materialen maken het grootste deel uit van de totale batterijkost, ongeveer 50%. De kathode neemt ongeveer 43% van de materiaalkosten voor haar rekening, en andere celmaterialen ongeveer 36%.
Verbetering van kathodematerialen zijn de belangrijkste innovaties, omdat de kathode de grootste component van de batterijkosten is. Dit drijft een sterke belangstelling voor de grondstoffenprijzen.
De meest voorkomende kathodematerialen voor elektrische voertuigen zijn nikkel-kobalt-aluminiumoxide dat wordt gebruikt in Tesla-voertuigen, nikkel-mangaan-kobaltoxide dat wordt gebruikt in de meeste andere elektrische voertuigen, en lithium-ijzerfosfaat dat wordt gebruikt in de meeste elektrische bussen.
Nikkel kobalt aluminium oxide heeft de laagste kosten-per-energie-inhoud en de hoogste energie-per-eenheid-massa, of specifieke energie, van deze drie materialen. Een lage kostprijs per energie-eenheid vloeit voort uit een hoge specifieke energie, omdat er minder cellen nodig zijn om een batterijpak te bouwen. Dit resulteert in een lagere kostprijs voor andere celmaterialen. Kobalt is het duurste materiaal in de kathode, zodat formuleringen van deze materialen met minder kobalt typisch leiden tot goedkopere batterijen.
Inactieve celmaterialen zoals tabs en houders zijn goed voor ruwweg 36% van de totale kosten van celmaterialen. Deze andere celmaterialen voegen geen energie-inhoud toe aan de batterij. Door het gebruik van inactieve materialen te beperken, kunnen het gewicht en de omvang van de batterijcellen worden verminderd zonder dat de energie-inhoud wordt verminderd. Dit stimuleert de belangstelling voor het verbeteren van het celontwerp met innovaties zoals tabloze batterijen zoals die welke door Tesla worden geplaagd.
De kosten van het batterijpak dalen ook aanzienlijk met een toename van het aantal cellen dat fabrikanten jaarlijks produceren. Naarmate meer EV-batterijfabrieken online komen, zouden schaalvoordelen en verdere verbeteringen in de fabricage en het ontwerp van batterijen moeten leiden tot verdere kostendalingen.
Tesla’s vernieuwde EV-batterijen
Op 22 september onthulde Tesla een reeks innovaties in de productie van lithium-ionbatterijen. Elke verandering heeft een effect op de uiteindelijke kosten van de batterijcellen en hun prestaties. Ons batterijkostenmodel laat zien dat de veranderingen die Tesla aanbrengt in de grootte en vorm van de batterijcel ertoe zullen leiden dat de twee elektroden van de batterij, de anode en de kathode, 80% van de kosten van de batterij voor hun rekening zullen nemen.
Eén verandering is een groter formaat voor de batterijcel, waardoor de hoeveelheid verpakkingsmateriaal afneemt en de hoeveelheid energie die elke cel kan opslaan toeneemt. De nieuwe vorm vermindert de bijdrage van hulpmaterialen aan de totale kosten van de batterijcel tot 15%, in plaats van 35%. Hulpmaterialen zijn alles behalve de anode, de kathode en de energieopslag-elektrolyt.
Daarmee komt het zwaartepunt van de kostenverlaging bij de elektroden te liggen. De kathode alleen maakt nu 55% van de kosten van de cel uit. Tesla beschreef verschillende wijzigingen in het proces voor de productie van kathodes, die de kosten zouden moeten verlagen, maar het is nog niet duidelijk met hoeveel.
Een andere verandering die het bedrijf onthulde, is een batterijontwerp dat tabbladen verwijdert, dat zijn stroken metaal die de anode en kathode verbinden met de buitenkant van de cel. Het verwijderen van lipjes verlaagt de kosten en verhoogt de verwerkingscapaciteit van de fabriek per uur. Hoe meer cellen kunnen worden gemaakt, hoe lager de kosten dankzij schaalvoordelen en verbeteringen in de fabricage.
Het zal waarschijnlijk ongeveer drie jaar duren voordat al deze veranderingen in productie gaan en de nieuwe batterijen verschijnen in EV’s met lagere prijzen, volgens het bedrijf.
Route naar prijs-pariteit
Voorspellen van een tijdlijn voor prijs-pariteit met ICE-voertuigen vereist voorspelling van een toekomstig traject van batterijkosten. Wij schatten dat verlaging van de grondstofkosten, verbetering van de prestaties en leren door productie samen waarschijnlijk zullen leiden tot batterijen met pakkosten van minder dan $80/kWh in 2025.
Aannemende dat batterijen een kwart van de EV-kosten vertegenwoordigen, levert een 100 kWh batterijpakket tegen $75 per kilowattuur een kostprijs op van ongeveer $30.000. Dit zou moeten resulteren in EV-stickerprijzen die lager zijn dan de stickerprijzen voor vergelijkbare modellen van auto’s die op gas rijden.
Abhinav Misalkar leverde een bijdrage aan dit artikel terwijl hij een afgestudeerde student was aan de Carnegie Mellon University.
Dit artikel is op 25 september bijgewerkt met details over Tesla’s nieuwe EV-batterijontwerp.