近年、電気自動車の販売台数は、価格の下落に伴って飛躍的に伸びている。 しかし、電気自動車の総所有コストが低いにもかかわらず、同等のガソリン車と比較して高いステッカー価格のため、電気自動車の採用は依然として制限されています。
EVと内燃機関車の価格が同等になるのは、今後10年間のうちのいつかだと思われる。 そのタイミングは、バッテリーコストという重要な要素にかかっている。 EVのバッテリーパックは車両コスト全体の約4分の1を占め、販売価格の最も重要な要素となっています。
バッテリーパックの価格は急速に低下しています。 一般的なEVのバッテリーパックは、10~100キロワット時(kWh)の電気を蓄える。 たとえば、三菱i-MIEVのバッテリー容量は16kWhで航続距離は62マイル、テスラ・モデルSのバッテリー容量は100kWhで航続距離は400マイルである。 2010年、EV用バッテリーパックの価格は1kWhあたり1,000ドルを超えていた。 それが2019年には1kWhあたり150ドルにまで低下した。 自動車業界の課題は、コストをさらに下げる方法を見つけ出すことです。
エネルギー省の業界目標は、バッテリーパックの価格を100ドル/kWh未満に、最終的には80ドル/kWh程度に下げることです。 これらのバッテリー価格帯では、EV のステッカー価格は同等の内燃エンジン車の価格よりも低くなる可能性があります。
その価格のクロスオーバーがいつ起こるかを予測するには、コスト変数である設計、材料、労働、製造能力および需要を説明するモデルが必要です。 また、これらのモデルは、研究者やメーカーがバッテリーのコストを削減するためにどこに焦点を当てているかを示しています。 カーネギーメロン大学の私たちのグループは、電気自動車のバッテリー製造のすべての側面を考慮したバッテリーコストのモデルを開発しました。 トップダウン型のモデルは、主に需要と時間に基づいてコストを予測します。 電池のコストを予測できる一般的なトップダウン・モデルのひとつに、ライトの法則があり、これは生産台数が増えるほどコストが下がることを予測するものである。 規模の経済と、産業界が時間をかけて獲得する経験が、コストを押し下げるのです。
ライトの法則は一般的なものです。 すべての技術にわたって機能するため、ソーラーパネルのコスト低下に基づいて、バッテリーのコスト低下を予測することが可能です。 しかし、ライトの法則は、他のトップダウン・モデルと同様に、コスト低下の原因を分析することはできません。 そのためには、ボトムアップ モデルが必要です。
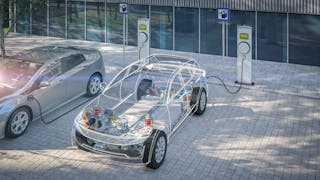
ボトムアップコストモデルを構築するには、バッテリーを作るために何が行われているかを理解することが重要です。 リチウムイオン電池は、正極であるプラス電極、負極であるマイナス電極、電解質、および端子やケーシングなどの補助部品で構成されています。
各部品には、材料費、製造費、組み立て費、工場のメンテナンスにかかる費用、諸経費などがかかる。 また、電気自動車の場合、電池は小さなセル群、つまりモジュールに統合され、それらを組み合わせてパックにする必要がある。
私たちのオープンソースのボトムアップのバッテリー コスト モデルは、バッテリーの製造プロセスそのものと同じ構造に従っています。 このモデルでは、電池の設計仕様、商品価格や労働力価格、製造工場や設備などの資本投資要件、間接費率、規模の経済を考慮した製造量など、電池製造プロセスへの入力をモデルへの入力として使用します。 これらの入力を使用して、製造コスト、材料コスト、および間接費を計算し、それらのコストを合計して最終的なコストを算出します。
コスト削減の機会
ボトムアップ コスト モデルを使用すると、バッテリーの各部分がバッテリー全体のコストに与える影響を分解し、これらの洞察を使用してバッテリーの革新が電気自動車のコストに与える影響を分析することができます。 材料は、電池の総コストのうち最も大きな割合を占めており、およそ50%を占めています。 正極は電池コストの最大の構成要素であるため、正極材料の改良は最も重要なイノベーションです。
電気自動車の最も一般的な正極材料は、Tesla 車に使用されているニッケル コバルト アルミニウム酸化物、その他のほとんどの電気自動車に使用されているニッケル マンガン コバルト酸化物、およびほとんどの電気バスに使用されているリン酸鉄リチウムです。
ニッケルコバルトアルミニウム酸化物は、これら3つの材料の中で、エネルギー含有量あたりのコストが最も低く、単位質量あたりのエネルギー、すなわち比エネルギーが最も高い。 比エネルギーが高いと、電池パックを作るために必要なセルの数が少なくなるため、単位エネルギーあたりのコストが低くなります。 その結果、他の電池材料も安価になる。 コバルトは正極の中で最も高価な材料なので、これらの材料のうちコバルトの含有量が少ないものは、一般的に安価な電池につながります。
タブや容器などの非活性セル材料は、セル材料コスト全体の約36%を占めています。 これらの他のセル材料は、電池にエネルギー内容を追加することはない。 したがって、非活性材料を減らすと、エネルギー含有量を減らすことなく、バッテリーセルの重量とサイズを減らすことができる。 このため、テスラが予告しているようなタブレス電池などのイノベーションによって、セル設計の改善に関心が集まっています。
電池パックのコストも、メーカーが年間に生産するセルの数が増えると、大幅に減少します。 より多くのEVバッテリー工場がオンラインになるにつれ、スケールメリットとバッテリー製造・設計のさらなる改善により、さらなるコストダウンが期待されます。
テスラのEV用電池刷新
9月22日、テスラはリチウムイオン電池の製造における一連の革新的な技術を明らかにした。 それぞれの変更は、最終的な電池セルのコストとその性能に影響を与える。 私たちのバッテリー コスト モデルでは、テスラがバッテリー セルのサイズと形状に対して行っている変更により、バッテリーのコストの 80% を陽極と陰極の 2 つの電極が占めることになります。
1 つの変更は、バッテリー セルのサイズを大きくし、梱包材を減らして各セルが蓄えられるエネルギー量を増加させるということです。 新しい形態では、バッテリー・セルの総コストに対する補助材料の寄与が35%から15%に減少しています。 補助材料とは、負極、正極、エネルギーを蓄積する電解質以外のすべてのものを指します。
これにより、コスト削減の焦点は電極に置かれます。 現在では、カソードだけでセルのコストの55%を占めています。 テスラは、正極の生産プロセスに対するいくつかの変更について説明しました。これはコストを下げるはずですが、どのくらい下げるかはまだ明らかではありません。
同社が発表した別の変更は、陽極と正極をセルの外側につなぐ金属のストリップであるタブを取り除くバッテリー設計です。 タブを取り除くことでコストを下げ、製造工場の時間当たりのスループットを向上させます。 9830>
これらの変更がすべて生産に移され、新しいバッテリーが低価格のEVに搭載されるまでには、おそらく3年ほどかかるだろうと同社は述べています。
価格パリティへの道
ICE車との価格パリティに向けたタイムラインを予測するには、バッテリーコストの将来の軌道を予測する必要があります。 私たちは、原材料コストの削減、性能の向上、製造による学習が相まって、2025年までにパックコストが80ドル/kWhを下回る電池になる可能性が高いと推定しています。
バッテリーがEVコストの4分の1を占めると仮定すると、100kWhのバッテリーパックを75ドル/kWhで計算すると、コストは約3万ドルになる。 この結果、EV のステッカー価格は、ガス自動車の同等モデルのステッカー価格よりも低くなるはずです。
Abhinav Misalkar は、カーネギー メロン大学の大学院生として、この記事に貢献しました。