Las ventas de vehículos eléctricos han crecido exponencialmente en los últimos años, acompañadas de un descenso de los precios. Sin embargo, la adopción de los vehículos eléctricos sigue estando limitada por su mayor precio de etiqueta en relación con los vehículos de gas comparables, a pesar de que el coste global de propiedad de los vehículos eléctricos es menor.
Es probable que los VE y los vehículos con motor de combustión interna alcancen la paridad de precios en algún momento de la próxima década. El momento depende de un factor crucial: el coste de la batería. El paquete de baterías de un VE representa aproximadamente una cuarta parte del coste total del vehículo, lo que lo convierte en el factor más importante del precio de venta.
Los precios de los paquetes de baterías han bajado rápidamente. Un paquete de baterías típico de un vehículo eléctrico almacena entre 10 y 100 kilovatios hora (kWh) de electricidad. Por ejemplo, el Mitsubishi i-MIEV tiene una capacidad de batería de 16 kWh y una autonomía de 62 millas, y el Tesla model S tiene una capacidad de batería de 100 kWh y una autonomía de 400 millas. En 2010, el precio de la batería de un vehículo eléctrico era de más de 1.000 dólares por kWh. Eso se redujo a 150 dólares por kWh en 2019. El reto para la industria del automóvil es averiguar cómo reducir aún más el coste.
El objetivo del Departamento de Energía para la industria es reducir el precio de los paquetes de baterías a menos de 100 dólares/kWh y, en última instancia, a unos 80 dólares/kWh. Con estos precios de las baterías, es probable que el precio de etiqueta de un VE sea inferior al de un vehículo de combustión comparable.
Predecir cuándo se producirá ese cruce de precios requiere modelos que tengan en cuenta las variables de coste: diseño, materiales, mano de obra, capacidad de fabricación y demanda. Estos modelos también muestran dónde centran sus esfuerzos los investigadores y fabricantes para reducir los costes de las baterías. Nuestro grupo de la Universidad Carnegie Mellon ha desarrollado un modelo de costes de baterías que tiene en cuenta todos los aspectos de la fabricación de baterías para vehículos eléctricos.
Desde abajo hacia arriba
Los modelos utilizados para analizar los costes de las baterías se clasifican en «descendentes» o «ascendentes». Los modelos descendentes predicen el coste basándose principalmente en la demanda y el tiempo. Un modelo descendente popular que puede predecir el coste de las baterías es la ley de Wright, que predice que los costes disminuyen a medida que se producen más unidades. Las economías de escala y la experiencia que adquiere una industria con el paso del tiempo reducen los costes.
La ley de Wright es genérica. Funciona en todas las tecnologías, lo que permite predecir el descenso de los costes de las baterías en función del descenso de los costes de los paneles solares. Sin embargo, la ley de Wright -como otros modelos descendentes- no permite analizar las fuentes de los descensos de costes. Para ello, es necesario un modelo ascendente.
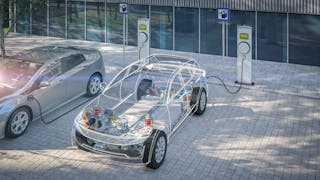
Para construir un modelo de costes ascendente, es importante entender lo que conlleva la fabricación de una batería. Las baterías de iones de litio constan de un electrodo positivo, el cátodo, un electrodo negativo, el ánodo y un electrolito, además de componentes auxiliares como los terminales y la carcasa.
Cada componente tiene un coste asociado a sus materiales, fabricación, montaje, gastos relacionados con el mantenimiento de la fábrica y gastos generales. En el caso de los vehículos eléctricos, las baterías también deben integrarse en pequeños grupos de celdas, o módulos, que luego se combinan en paquetes.
Nuestro modelo de costes de baterías, de código abierto y ascendente, sigue la misma estructura que el propio proceso de fabricación de baterías. El modelo utiliza como insumos del proceso de fabricación de baterías las especificaciones de diseño de las mismas, los precios de las materias primas y de la mano de obra, los requisitos de inversión de capital como las plantas de fabricación y los equipos, las tasas de gastos generales y el volumen de fabricación para tener en cuenta las economías de escala. Utiliza estos datos para calcular los costes de fabricación, los costes de los materiales y los gastos generales, y estos costes se suman para obtener el coste final.
Oportunidades de reducción de costes
Usando nuestro modelo de costes ascendente, podemos desglosar las contribuciones de cada parte de la batería al coste total de la misma y utilizar estos datos para analizar el impacto de las innovaciones en el coste del vehículo eléctrico. Los materiales representan la mayor parte del coste total de la batería, alrededor del 50%. El cátodo representa alrededor del 43% del coste de los materiales, y otros materiales de la celda suponen alrededor del 36%.
Las mejoras en los materiales del cátodo son las innovaciones más importantes, porque el cátodo es el mayor componente del coste de la batería. Esto provoca un gran interés en los precios de las materias primas.
Los materiales catódicos más comunes para los vehículos eléctricos son el óxido de níquel-cobalto-aluminio utilizado en los vehículos Tesla, el óxido de níquel-manganeso-cobalto utilizado en la mayoría de los demás vehículos eléctricos y el fosfato de hierro-litio utilizado en la mayoría de los autobuses eléctricos.
El óxido de níquel-cobalto-aluminio tiene el menor coste por contenido energético y la mayor energía por unidad de masa, o energía específica, de estos tres materiales. El bajo coste por unidad de energía se debe a la alta energía específica, ya que se necesitan menos celdas para construir una batería. Esto se traduce en un menor coste de los otros materiales de las pilas. El cobalto es el material más caro dentro del cátodo, por lo que las formulaciones de estos materiales con menos cobalto suelen dar lugar a baterías más baratas.
Los materiales de las celdas inactivas, como las lengüetas y los contenedores, representan aproximadamente el 36% del coste total de los materiales de las celdas. Estos otros materiales de la celda no añaden contenido energético a la batería. Por lo tanto, la reducción de los materiales inactivos reduce el peso y el tamaño de las celdas de la batería sin reducir el contenido energético. Esto impulsa el interés por mejorar el diseño de las celdas con innovaciones como las baterías sin lengüetas, como las que está anunciando Tesla.
El coste del paquete de baterías también disminuye significativamente con un aumento del número de celdas que los fabricantes producen anualmente. A medida que se pongan en marcha más fábricas de baterías para vehículos eléctricos, las economías de escala y las nuevas mejoras en la fabricación y el diseño de las baterías deberían conducir a un mayor descenso de los costes.
Las renovadas baterías para vehículos eléctricos de Tesla
El 22 de septiembre, Tesla reveló una serie de innovaciones en la fabricación de baterías de iones de litio. Cada cambio tiene un efecto sobre el coste final de las células de la batería y su rendimiento. Nuestro modelo de coste de la batería muestra que los cambios que Tesla está realizando en el tamaño y la forma de la célula de la batería harán que los dos electrodos de la batería, el ánodo y el cátodo, representen el 80% del coste de la batería.
Un cambio es un tamaño más grande para la célula de la batería, que reduce la cantidad de material de embalaje y aumenta la cantidad de energía que cada célula puede almacenar. La nueva forma reduce la contribución de los materiales auxiliares al coste total de la célula de la batería al 15%, frente al 35%. Los materiales auxiliares son todo lo que no sea el ánodo, el cátodo y el electrolito que almacena energía.
Esto hace que la reducción de costes se centre en los electrodos. Sólo el cátodo representa ahora el 55% del coste de la célula. Tesla describió varios cambios en el proceso de producción de los cátodos, que deberían reducir los costes, pero aún no está claro en qué medida.
Otro cambio que la compañía dio a conocer es un diseño de batería que elimina las lengüetas, que son tiras de metal que unen el ánodo y el cátodo con el exterior de la célula. La eliminación de las lengüetas reduce el coste y aumenta el rendimiento por hora de la planta de fabricación. Cuantas más celdas se puedan fabricar, menor será el coste gracias a las economías de escala y a las mejoras en la fabricación.
Según la empresa, probablemente se necesiten unos tres años para que todos estos cambios entren en producción y las nuevas baterías aparezcan en los vehículos eléctricos de menor precio.
Camino hacia la paridad de precios
Predecir un plazo para la paridad de precios con los vehículos con motor de combustión interna requiere prever una trayectoria futura de los costes de las baterías. Estimamos que la reducción de los costes de las materias primas, las mejoras en el rendimiento y el aprendizaje por parte de la fabricación, en conjunto, probablemente conduzcan a baterías con costes de los paquetes por debajo de los 80 dólares/kWh en 2025.
Suponiendo que las baterías representen una cuarta parte del coste del VE, un pack de baterías de 100 kWh a 75 dólares por kilovatio hora supone un coste de unos 30.000 dólares. Esto debería traducirse en precios de etiqueta de los VE inferiores a los de modelos comparables de coches de gasolina.
Abhinav Misalkar colaboró en este artículo mientras era estudiante de posgrado en la Universidad Carnegie Mellon.
Este artículo se ha actualizado el 25 de septiembre con detalles sobre el nuevo diseño de baterías para VE de Tesla.